Aluminum vs. Copper Wiring: What You Need to Know
When you're faced with the choice between aluminum and copper wiring, it's important to weigh the pros and cons carefully. Each material has its unique advantages, from conductivity to cost, and understanding these differences can significantly impact your project's success. You might be surprised to find out how factors like weight and corrosion resistance play into your decision-making process. As you consider your options, think about what really matters for your specific needs—this choice could affect both safety and efficiency in ways you might not expect.
Overview of Wiring Materials
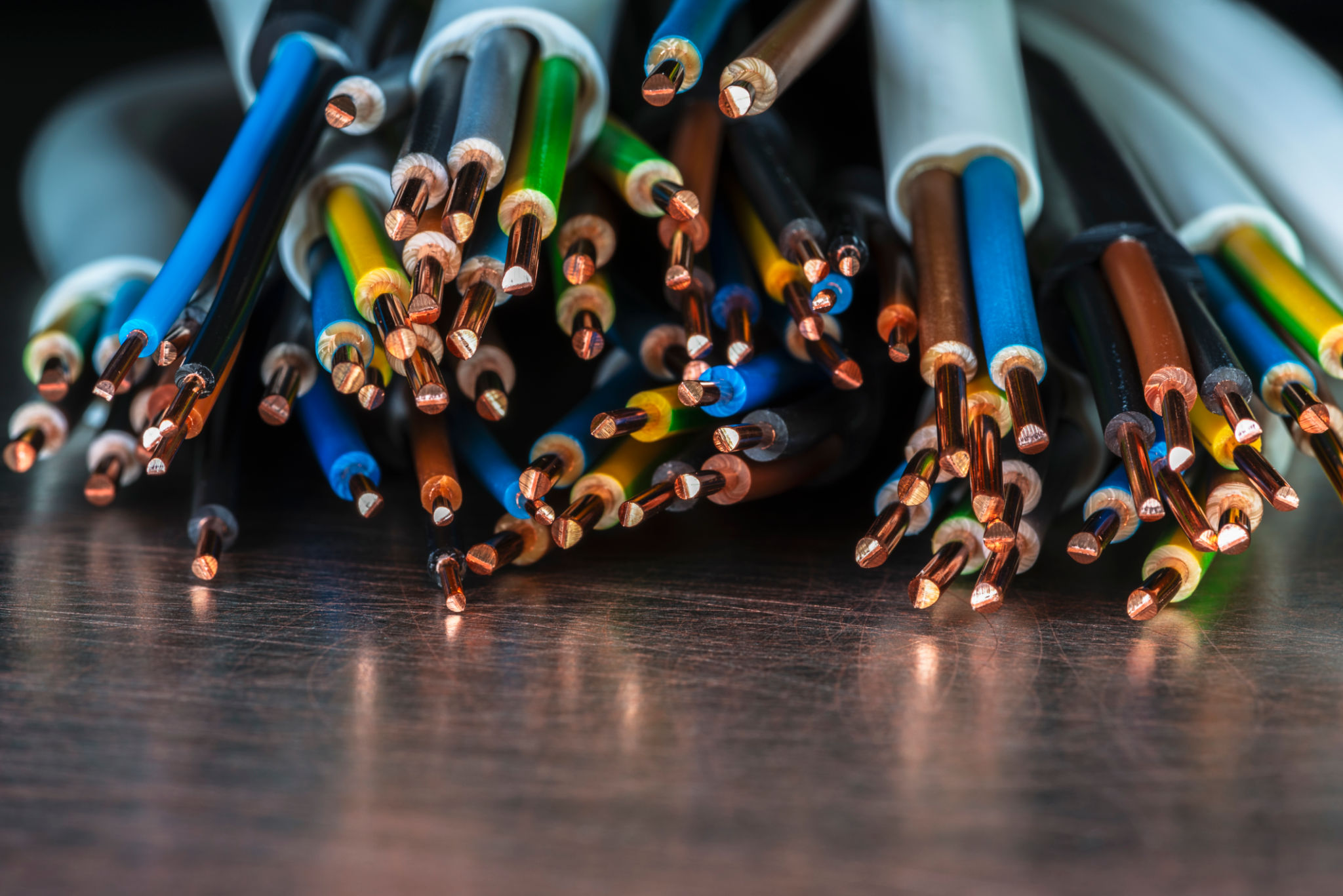
When it comes to wiring materials, you'll find two primary contenders: aluminum and copper. Each material presents unique characteristics that affect wiring types and installation techniques. Copper, known for its superior conductivity, is commonly used in residential and commercial applications. It's flexible, allowing for easier handling during installation, and it resists corrosion, which enhances longevity. However, copper's higher cost can be a significant factor in project budgeting.
On the other hand, aluminum is lightweight and less expensive, making it an appealing choice for large-scale installations, such as overhead power lines. Its lower conductivity requires larger gauge sizes compared to copper, which can influence the design and installation techniques you choose. You'll need to consider the specific wiring types and configurations suited for aluminum, as it demands careful handling to prevent issues like oxidation and breakage at connections.
Ultimately, your choice between aluminum and copper wiring will depend on factors like application, budget, and long-term performance expectations. Analyzing the materials' properties and understanding the implications for installation techniques is crucial for making an informed decision.
Conductivity and Performance
When comparing aluminum and copper wiring, you'll notice significant differences in electrical conductivity. Copper typically outperforms aluminum in this regard, providing superior efficiency in electrical systems. Additionally, understanding heat resistance and long-term performance factors is crucial for making the right choice for your wiring needs.
Electrical Conductivity Comparison
Comparing the electrical conductivity of aluminum and copper reveals significant differences that affect their performance in various applications. Historically, copper has been the preferred choice for electrical wiring due to its higher conductivity standards, which measure how well a material can transmit electric current. Copper's conductivity is approximately 59siemens/meter, making it around 60% more conductive than aluminum, which stands at about 37siemens/meter.
This difference means that for the same amount of current, a copper wire can be thinner than an aluminum wire while still maintaining similar performance levels. Consequently, in applications requiring high efficiency and minimal energy loss, copper's superior conductivity often makes it the preferred material, especially in residential and commercial wiring.
However, aluminum's lighter weight and lower cost have led to its increased use in certain applications, such as overhead power lines and large-scale installations. Despite its lower conductivity, aluminum can still meet specific needs, provided the wiring is appropriately sized to compensate for its inferior performance. Understanding these conductivity differences is crucial when selecting the right material for your electrical needs.
Heat Resistance Differences
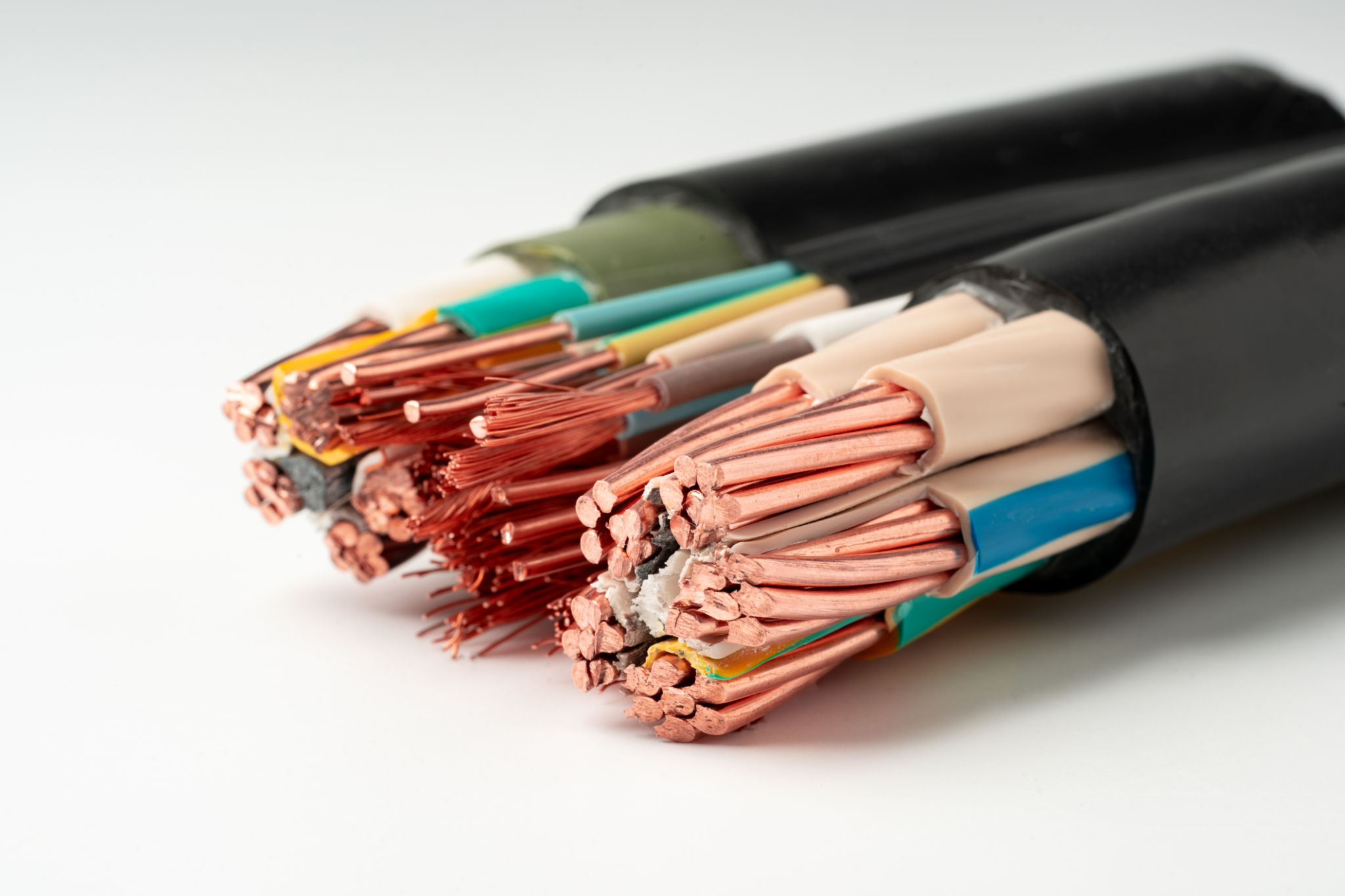
Heat resistance plays a crucial role in determining the performance and safety of electrical wiring materials like aluminum and copper. When evaluating these two metals, you must consider how their thermal properties impact functionality and installation. Aluminum tends to have a higher thermal expansion coefficient, which means it expands more when heated. This can lead to complications, especially if proper insulation requirements aren't met.
Here are some critical points to keep in mind:
- Thermal Conductivity: Copper has superior thermal conductivity, allowing it to dissipate heat more efficiently and reducing the risk of overheating.
- Expansion Issues: The significant thermal expansion of aluminum can lead to loose connections, increasing the likelihood of arcing or failure if not properly managed.
- Insulation Compatibility: Different insulation materials may be required based on the heat resistance of the wiring; copper generally requires less extensive insulation due to its heat-dissipating properties.
Ultimately, understanding these heat resistance differences is vital for ensuring the safety and reliability of your electrical systems. Choosing the right material affects not just performance but also long-term maintenance needs.
Long-Term Performance Factors
Evaluating the long-term performance of electrical wiring materials involves examining factors like conductivity and overall operational efficiency. Copper wiring typically excels in conductivity, offering lower resistance over time. This characteristic translates into enhanced energy efficiency and reduced heat generation, which is critical for long-term reliability. On the other hand, aluminum wiring presents unique installation challenges due to its tendency to expand and contract, which can lead to loose connections and potential failures if not installed correctly.
When considering performance longevity, copper's superior conductivity provides a significant advantage. It maintains performance levels even under heavy loads, whereas aluminum may require more frequent inspections and maintenance to ensure continued efficacy. Additionally, copper's resistance to corrosion contributes to its durability over the years, enhancing its long-term reliability in various environments.
In contrast, while aluminum can be a cost-effective option, its performance may degrade faster if proper installation techniques aren't employed. Understanding these factors is essential for making informed decisions about wiring materials, especially when you're looking to invest in a system that will perform reliably for years to come.
Cost Comparison

When considering the cost of wiring materials, aluminum often presents a more budget-friendly option than copper. The initial price of aluminum is generally lower, making it an attractive choice for large-scale projects. However, it's crucial to factor in price fluctuations and material availability, as these can significantly influence overall costs.
- Aluminum wiring typically costs 30-50% less per pound than copper.
- The price of copper can be volatile, affected by global demand and mining output, leading to unpredictable budgeting.
- Aluminum's abundant supply often results in more stable pricing, reducing long-term financial risk.
While aluminum may save you money upfront, consider potential long-term implications, such as maintenance costs and lifespan. Copper, though more expensive, often offers superior conductivity and durability, which might justify its higher price in specific applications. Ultimately, your choice will depend on the balance between initial savings and long-term performance. Assessing the current market conditions, including price fluctuations and material availability, will provide you with a clearer picture of which option aligns best with your project's financial and performance goals.
Weight and Flexibility
The weight and flexibility of wiring materials are critical factors to consider in any electrical installation. Aluminum wiring is significantly lighter than copper, which can improve weight distribution in overhead installations. This lighter weight can reduce the stress on structural components and facilitate easier handling during installation. Conversely, copper, while heavier, offers superior flexibility benefits. Its malleability allows for tighter bends and shapes, which can be advantageous in constrained spaces or complex configurations.
When planning your installation, think about the specific requirements of your project. If you're working in areas with weight restrictions, aluminum may be the better choice. However, if your installation requires extensive bending or routing through tight spaces, the flexibility of copper could save you time and reduce the risk of damaging the wire.
It's also essential to consider the long-term implications of weight and flexibility in your wiring choices. While both materials have their strengths, understanding how these factors will affect your specific application can lead to more efficient and reliable electrical systems. By evaluating weight distribution and flexibility benefits, you can make a more informed decision that aligns with your installation needs.
Corrosion Resistance
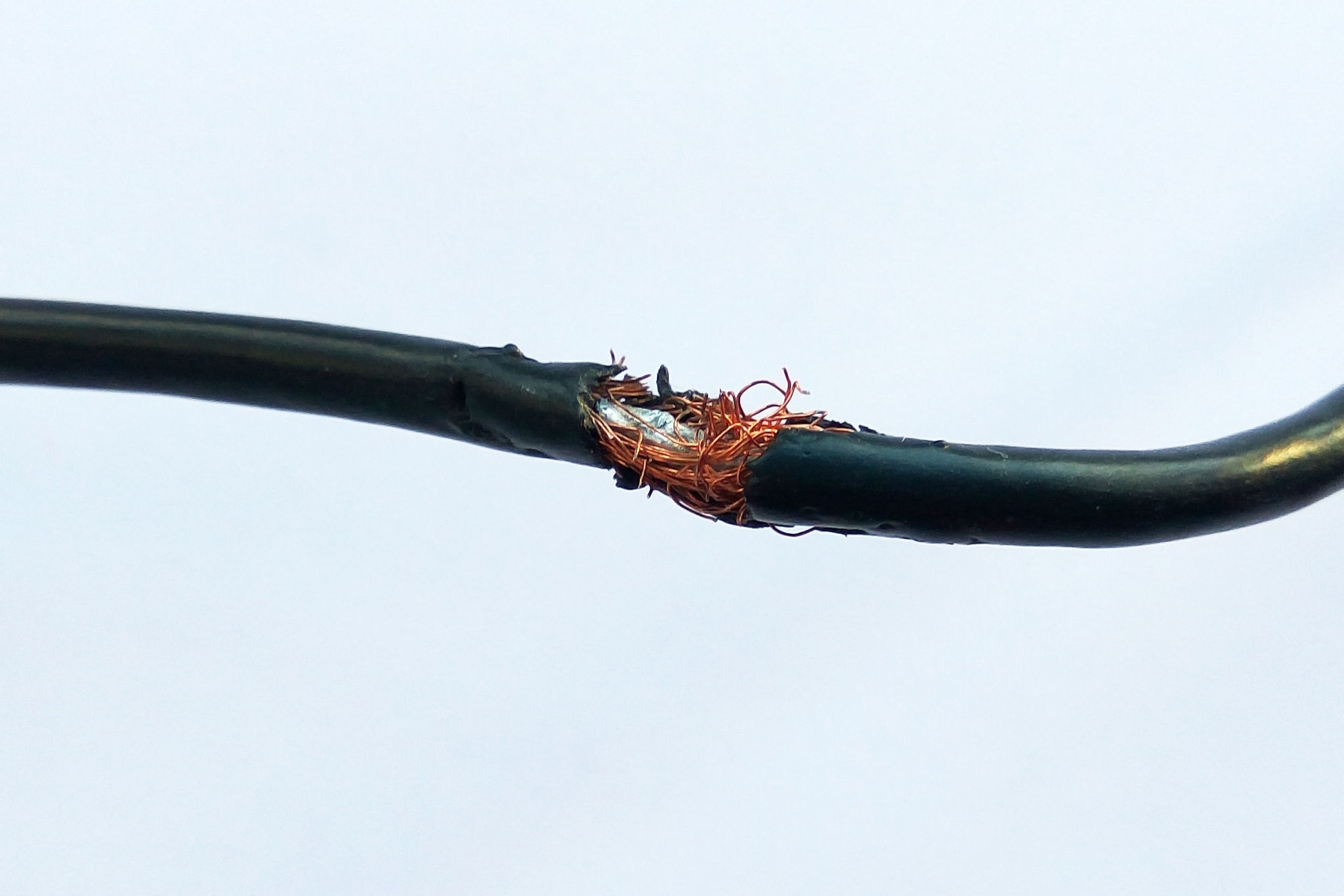
When evaluating corrosion resistance, it's essential to consider environmental factors that can accelerate deterioration of wiring materials. Aluminum tends to oxidize when exposed to moisture and pollutants, impacting its longevity, while copper can develop patina that offers some protection. Understanding these differences is crucial for maintenance considerations and ensuring the reliability of your electrical systems.
Environmental Factors Impacting Corrosion
Corrosion resistance in wiring materials like aluminum and copper is significantly influenced by environmental factors such as humidity, temperature, and exposure to corrosive agents. Different corrosion types, including galvanic, pitting, and uniform corrosion, can occur under varying environmental conditions, impacting the longevity of your wiring system.
To mitigate corrosion risks effectively, consider the following factors:
- Humidity Levels: High humidity can accelerate corrosion, particularly for copper, which is susceptible to copper oxides formation.
- Temperature Fluctuations: Extreme temperatures can alter the physical properties of wiring materials, leading to increased corrosion rates.
- Chemical Exposure: Proximity to chemicals or pollutants can exacerbate corrosion processes, particularly in industrial environments.
Understanding these environmental factors helps you make informed decisions about wiring materials. For instance, while copper may provide superior electrical conductivity, its susceptibility to certain types of corrosion under specific environmental conditions could necessitate more frequent inspections and maintenance. Conversely, aluminum, although less conductive, offers better resistance to certain corrosion types, potentially leading to lower maintenance requirements in specific environments. Therefore, assessing your unique environmental conditions is crucial for selecting the appropriate wiring material.
Longevity and Maintenance Considerations
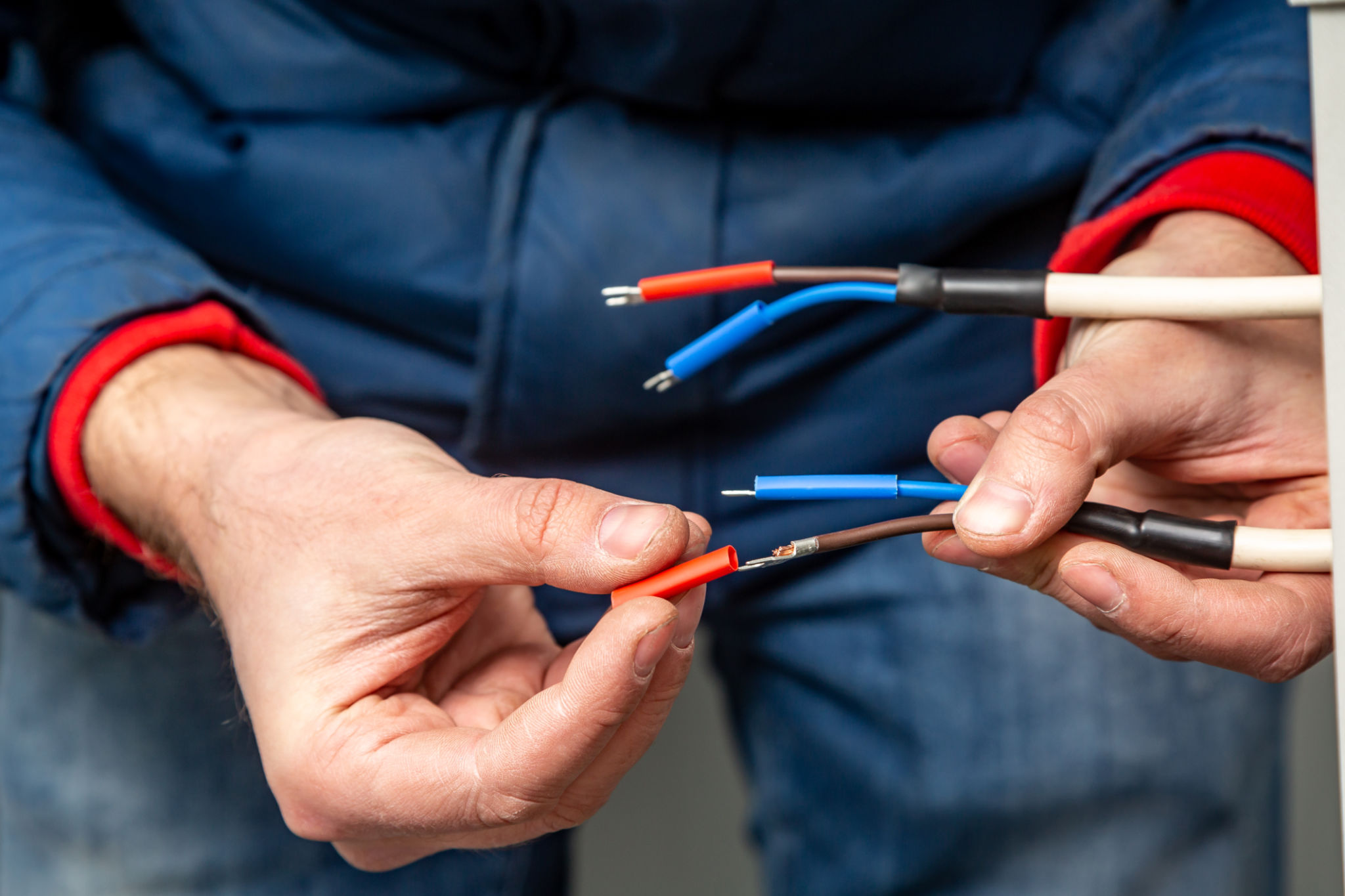
While selecting wiring materials, understanding longevity and maintenance considerations is essential for ensuring optimal performance over time. Corrosion resistance plays a pivotal role in determining how long your wiring can last and how often you'll need to conduct maintenance.
Copper wiring generally exhibits excellent corrosion resistance, particularly when coated with appropriate insulation types, such as PVC or thermoplastic materials. These insulations create a barrier that minimizes exposure to moisture and corrosive elements. On the other hand, aluminum wiring is more susceptible to oxidation, which can lead to increased resistance and potential overheating if not regularly inspected and maintained.
Implementing effective repair techniques is crucial for both materials. For copper, ensuring tight connections and minimizing exposure helps maintain conductivity. With aluminum, using anti-oxidant compounds during installation can help mitigate corrosion.
Ultimately, the choice between aluminum and copper wiring should factor in not just initial costs but also long-term maintenance needs. You'll want to consider how each material's longevity aligns with your specific requirements, ensuring that your wiring remains reliable over time, regardless of environmental challenges.
Safety Considerations
Safety considerations surrounding aluminum and copper wiring are critical due to their distinct electrical properties and susceptibility to different types of deterioration. With differing rates of thermal expansion and conductivity, the choice between the two can significantly impact installation safety and long-term performance.
You must be aware of the potential hazards associated with each type of wiring. Aluminum, for instance, is prone to insulation degradation, which can lead to fire hazards and electrical accidents. Grounding issues can also arise, making it essential to ensure proper connections. Copper, while more stable, can still experience repair challenges related to corrosion over time.
Key safety concerns include:
- Fire Hazards: Both materials can present risks if not installed or maintained properly, particularly in high-load situations.
- Electrical Accidents: Poor connections and degradation can lead to short circuits and electrocution risks.
- Code Compliance: Adhering to local electrical codes is crucial for minimizing safety risks associated with wiring.
Ultimately, understanding these factors will help you make informed decisions that prioritize safety and compliance in your electrical systems.
Installation Process

Understanding the safety considerations of aluminum and copper wiring sets the stage for their installation process. When you're preparing for installation, selecting the appropriate wire gauge is crucial. For aluminum wiring, you typically need a larger gauge compared to copper to carry the same current safely. For example, a 12-gauge copper wire can be substituted with a 10-gauge aluminum wire.
Next, familiarize yourself with the specific installation techniques for each type. Copper wiring is more flexible and easier to manipulate, which can simplify installation in tight spaces. However, aluminum requires special attention to connections; using anti-oxidant compounds on aluminum wire connections can prevent corrosion and ensure a secure connection.
Always check local codes and regulations, as they may dictate specific installation practices. Use proper tools and techniques, such as torque wrenches for connections, to avoid over-tightening, which can damage the wire. Lastly, ensure that you're following the manufacturer's guidelines for both wire types to maintain compliance and safety throughout the installation process. By focusing on these details, you'll enhance the reliability of your electrical system.
Lifespan and Durability
When assessing the lifespan and durability of aluminum versus copper wiring, it's essential to consider their inherent properties and how they respond to environmental factors. Aluminum wiring is lighter and generally more cost-effective, but it faces challenges such as aluminum fatigue, which can lead to structural weaknesses over time. This fatigue often arises from cyclical temperature changes, causing expansion and contraction that may lead to failures.
Copper wiring, on the other hand, boasts superior conductivity and longevity. However, it's not without its issues; copper oxidation can occur when exposed to moisture and air, resulting in a layer of copper oxide that can impede electrical flow and increase resistance.
Consider these points when evaluating lifespan and durability:
- Corrosion Resistance: Copper generally resists corrosion better than aluminum, enhancing its lifespan.
- Thermal Conductivity: Copper's higher thermal conductivity contributes to its durability under heavy loads.
- Joint Reliability: Aluminum requires more careful connections to prevent loosening, while copper provides more reliable joints.
Ultimately, your choice should align with your specific electrical needs and environmental conditions.
Environmental Impact

The choice between aluminum and copper wiring extends beyond performance metrics; it also encompasses significant environmental considerations. When you evaluate these materials, consider their environmental footprints, particularly in terms of energy efficiency and recycling methods.
Aluminum wiring, while lighter and generally cheaper, requires more energy to produce compared to copper. However, aluminum's recycling methods are quite efficient, allowing for a lower overall environmental impact when recycled properly. In fact, recycling aluminum uses about 95% less energy than producing new aluminum from ore.
Copper, on the other hand, boasts superior conductivity and durability, which can translate into greater energy efficiency in wiring systems. However, its extraction and processing are energy-intensive, leading to a higher carbon footprint. The recycling of copper is also highly effective, reclaiming about 90% of the energy initially used in its production.
Ultimately, your choice should weigh the benefits of energy efficiency against the effectiveness of recycling methods. By understanding these dynamics, you can make a more informed decision that aligns with your environmental goals and values.
Conclusion
In choosing between aluminum and copper wiring, you must weigh performance against cost and maintenance. Notably, copper's conductivity is about 60% higher than aluminum's, making it the preferred choice for high-demand applications. However, aluminum's lower cost and lighter weight can be advantageous in large-scale installations. Remember, the right material depends on your specific project needs, budget, and long-term goals, ensuring safety and efficiency in your wiring choices. Make an informed decision for optimal results.